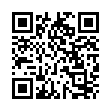
The Annotated Inspection Checklist (2024)
Based on 2024 FRC Inspection Checklist, Rev 3.
Size and Weight π
β ROBOT Weight - Must be β€ 125 lbs. (~56kg) excluding BUMPERs and battery. β R103
β Total Inspected Weight - ROBOT + swappable mechanisms β€150 lbs. β I103
β BUMPER Weight - Must be β€ 15 pounds (~6kg). β R407
Teams should join the weigh-in queue as soon as possible. For weigh-in, the bumpers should be off, and battery out. Bring both sets of bumpers. Bring any additional mechanisms you may be installing on your robot. Weigh each set of bumper separately, together with all removable mounting hardware. Do not step on the scales.
β FRAME PERIMETER - Frame must be non-articulated. Minor protrusions β€1/4β (6mm) OK. β R101
β STARTING CONFIGURATION - Parts may not extend past the vertical projection of the FRAME PERIMETER. β R102
This will usually be checked in the pit. If parts of your superstructure are close to the frame perimeter, the inspector may ask to borrow a straight edge, so you should have one ready.
β Starting Volume - FRAME PERIMETER β€ 120in. (~304 cm), height β€ 48 in. (~121 cm) β R104
These will usually be measured at the inspection table after weigh-in. The frame perimeter is measured using a fabric tape measure. Feel free to assist the inspector in making this measurement as their arms may be too short to go around the robot. The height will usually be assessed using a stick with a crossbar. If itβs close, you may be asked to place the robot on the floor for this measurement.
β Playing Configuration - ROBOT may not extend beyond the FRAME PERIMETER by more than 12 in. (~30 cm) β R105
The inspector will ask you to demonstrate the robotβs maximum horizontal extension. If the robot is physically capable of exceeding 12β, then you will be asked to demonstrate software control after the power on checks.
Inspectors will not normally measure the robotβs maximum vertical extension. This is primarily assessed by referees during a match, and inspectors will be asked to measure it only if the head referee requests.
Bumpers π
β Coverage - BUMPER segments protect the entire FRAME PERIMETER, any gaps between segments < 1β2β (~1.3cm) β R401
Full coverage bumpers are required this year. Using a gap for strategic advantage will invite additional scrutiny.
β Hard BUMPER parts - Defined by BUMPER backing, may not extend >1β (~25mm) beyond ROBOT frame. β R408
Remember that this 1β allowance includes both the β€ΒΌβ gap and the nominal ΒΎβ backing.
β Support - No BUMPER segment may be unsupported by ROBOT structure/frame for a length > 8β (~20cm), Gaps β€ 1β4β (~6mm) may be wider than 8β. BUMPER segments must be supported by at least 1β2β (~13mm) of ROBOT frame at each end (< 1β4β (~6mm) gap between segment and frame are OK) β R410 & Fig 8-8
βSupportβ here refers to horizontal support, not vertical. Your inspector may have a tool to assist in determining if a gap is larger than ΒΌβx8β.
β Corners - Must be filled with pool noodle such that no βhard partsβ are exposed. β R409
β Wood backing - Must use 3β4β (~19mm) thick x 5Β±1β2β (~127 mm Β± 12.7 mm) tall plywood, OSB, or solid robust wood backing w/out extraneous holes affecting structural integrity. (shallow clearance pockets and/or access holes are acceptable) β R408-A
β Pool Noodles - Must use a pair of stacked 21β2β nominal (21β8β β 2 3β4β) pool noodles. Pool noodles may be any shape cross section, solid or hollow, but both must be identical in shape and density. Must use a durable cloth cover secured as in Fig 8-6 cross section. β R408-C, R408-D
β Color - Must be able to display red or blue to reflect alliance color. β R405
β Team number - displayed with Arabic numerals, min. font 4β (~11cm) tall x 1β2β (~13mm) stroke, in white, and be easily read from approximately 60β (1828 cm) when walking around the perimeter of the ROBOT. No logos may be used for numerals. FIRST logos comparable to 2024 Virtual KOP may also be applied β R405, R405
Inspectors will ask to see the numbers on all four sides of each bumper. If you have a reversible bumper cover, they will ask to see that demonstrated.
β Attachment - Must be securely mounted when attached and be easily removable for inspection. β R404, R408-G
If your frame perimeter was measured during weigh-in, then the inspector will probably want you to attach a set of bumpers before they get to your pit. Remember that your bumpers may be subjected to both horizontal and vertical forces during a match. The inspector will likely perform a βlift testβ where they gently apply about 25lbs of force upwards to each segment. Not only should the bumper stay attached, but it should also stay within 7Β½β of the ground.
β Height - When ROBOT is on a flat floor, all BUMPER segments must reside entirely between the floor and 71β2β (~19cm) above floor. They may not be articulated. β R402, R403
Remember that any mounting hardware that is attached to the bumpers or which is removable should be within 7Β½β of the floor.
Mechanical π
β No Sharp Edges or Protrusions that are a hazard for participants, ROBOTS, ARENA, or FIELD. - β R202
The inspector will usually run their hand over the robot, looking for sharp edges, especially any that face outwards.
β No Prohibited Materials - E.g. sound, lasers (other than class 1), flammable gases, or untreated hazardous materials β R203
A typical laser pointer is Class 3A and is therefore not permitted on an FRC robot.
If you have added ballast, make sure that any lead weights are sealed, e.g. painted.
β No Unsafe Energy Storage Devices - Carefully consider safety of all stored energy or pneumatic systems β R203
The inspector may ask about springs. Remember that your climber or intake might contain springs.
β No Risk of Damage to Other ROBOTS - E.g. damaging, entangling, upending or adhering β G419, R203
Avoid having loops of wire near the frame perimeter.
β No Risk of Damage to FIELD - E.g. metal cleats on traction devices or sharp points on frame. β R201, R202
The inspector may examine the bottom of the robot for protruding bolts. Under-bumper intakes that come close to the floor will invite additional scrutiny.
β No Risk of damage to Game Pieces - areas interacting with game pieces free of sharp or damaging surfaces β R206
The inspector will ask you to indicate the path of game pieces through the robot and will be looking for things like protruding bolts and sharp edges.
β Decorations - Cannot interfere with other ROBOTSβ electronics or sensors, be in spirit of βGracious Professionalismβ β R203
Primarily the inspector will be looking for April Tags and bright lights.
β End Game - GAME PIECES can be removed from ROBOT and ROBOT from FIELD without power. β R204
β STAGE Chain - ROBOT not designed to reduce working length of field chain (e.g. create slack or twist chain) β R106
β End Game - GAME PIECES can be removed from ROBOT and ROBOT from FIELD without power. β R204
β STAGE Chain - ROBOT not designed to reduce working length of field chain (e.g. create slack or twist chain) β R106
Electrical π
β Components - None may be modified, except for motor mounting and output shaft, motor wires may be trimmed, window motor locking pins may be removed, and certain devices may be repaired with parts identical to the originals. PDP/PDH fuses may be replaced with identical fuses only. Servos may be modified per manufacturerβs instructions. β R503, R710
The inspector will likely ask you to describe any changes you have made.
β Battery - A single 12 volt, 17-18.2 Ah ROBOT battery, securely fastened inside ROBOT. β R601, R605, R606
The inspector will expect you to secure the battery in the robot and may attempt to lift it out. Tape and/or zip ties are not usually considered to be acceptable ways to secure the battery.
Please remember to secure your battery on the field (G411FC). If your battery strap breaks or is lost, ensure it is replaced with an acceptable alternative.
The inspector will also check that your battery is fully insulated (R607) and will probably ask to see all of your batteries. Battery posts should not have exposed metal.
If you have applied labels to your battery, the inspector may advise you not to cover the vents.
R604 (Charge batteries at a safe rate) prohibits the use of fast-chargers at events.
β Other Batteries - Integral to COTS computing device or camera or COTS USB < 100Wh (20,000mAh at 5V) and 5 Amp max output per port used for COTS computing device and accessories only. Small batteries for CMOS/RTC are OK. β R602
β PDP/PDH Visibility - The single PDP/PDH, and PDP/PDH breakers must be easily visible for inspection. β R613
If your PDP/PDH is on the underside of the robot, you will be asked to invert it for inspection. The inspector may have to switch back and forth between top and bottom.
If your PDP/PDH is behind a panel, you will probably be asked to remove it for inspection.
If the PDP/PDH is hard to examine, this will likely cause delay in inspection.
β Main Breaker Accessibility - The single 120A main breaker must be readily accessible with labeling preferred. β R612
The main breaker should be easy to find and accessible without putting your hand through a moving mechanism. It is not necessary that it be exposed to the possibility of accidental operation by other robots.
The inspector will also check that your main breaker is fully insulated (R607). The two power terminals should not have exposed metal.
β Allowable PD Breakers - Only VB3-A, MX5-A, MX5-L Series Snap-Action breakers or REV Robotics ATO (40A or lower) may be inserted in the PDP/PDH β R619
If you run out of the colored breakers that come with the PDH, remember you may also use the smaller black breakers from the PDP.
β ROBOT Radio - A single OpenMesh OM5P-AN or OM5P-AC radio powered via a VRM +12 volt, 2 amp output or REV RPM. The VRM/RPM must connect to the dedicated +12 volt output on the PDP/PDH. Radio LEDs are easily visible β R616, R702, R707, R708
You must use either a VRM or an RPM to power the radio (R616).
Dual power (through both barrel jack and POE) is only for VRM power; you cannot do dual power if you are using an RPM (R616, R617).
POE must use the Ethernet port next to the barrel connector, which is also where the robotRIO must be connected (directly or indirectly) (R703).
If youβre using a VRM, then you canβt use the other 12V/2A terminals for a non-radio purpose.
The VRM or RPM should be connected to either:
- PDP: The dedicated terminals (marked in green) on the PDP using at least 18 AWG wire
- PDH: Any of the non-switchable channels (20β22) (not marked red) on the PDH with a 10A (red) fuse, using at least 22 AWG wire.
β CAN BUS - The roboRIO and PDP/PDH must be connected via CAN wiring even if no other CAN devices are used. β R716
β roboRIO Power - Only the roboRIO must be connected to dedicated power terminals on PDP/PDH. β R615
With a PDP, this means the dedicated terminals (marked in blue) with an associated 10A (red) fuse. With a PDH, this means any of the non-switchable channels (20β22) with an associated 10A (red) fuse.
β Wire Size Minimum and Breaker Size - obey the wiring size conventions.
- β All wire from battery to main breaker to PDP/PDH must be min 6 AWG (7 SWG or 16mm2) wire β R609 & Fig.8-9
- β 40 amp breakers must have min 12 AWG (13 SWG or 4 mm2) wire connected β R622
- β 30 amp breakers must have min 14 AWG (16 SWG or 2.5 mm2) wire connected β R622
- β 20 amp breakers must have min 18 AWG (18 SWG or 1 mm2) wire connected β R622
The breaker/fuse protects the wire, not the other way around.
Certain devices (e.g. linear actuators, relays, PCM/PH, additional VRMs) must be on 20A or 10A regardless of wire gauge.
PDP fuses should be one 20A (yellow) and one 10A (red) as printed on the PDP itself.
PDH fuses are limited to 15A (blue) unless the robot has pneumatics.
Pneumatics may be on a 20A (yellow) fuse, but may also be on a breaker.
Looking at PDH fuses, you should expect to see two reds (radio and roboRIO) in the first three slots, and then up to two blues.
The REV Mini Power Module (MPM) is not directly addressed in the rules, but manufacturer specs indicate it should be connected to a 40A breaker and fitted with 15A (blue) or lower fuses. The MPM cannot be used to power either the radio (directly or indirectly) or the roboRIO. It does not provide regulated power.
β Wire Colors - All power wire must be color coded - red, yellow, white, brown, or black w/stripe for +24, +12, +5 VDC supply (positive) wires and black or blue for common (negative) for supply return wires except original wire by manufacturer β R624
Separated zip wire often presents as striped (e.g. red stripe on black) but this is legal.
β Copper Wire Only - All wire used on ROBOT must be copper wire. (Signal wire excluded) β R622
Watch out for any wire marked βCCAβ (copper coated aluminum) as this is not legal.
β 1 Wire per WAGO - Only 1 wire may be inserted in each WAGO terminal. Splices and/or terminal blocks, may be used to distribute power to multiple branch circuits but all wires in the splice are subject to the wire size rules β R618
β Motors - Only motors listed per Table 8-1, there may be no more than four (4) propulsion motors β R501, R502
β Actuators - Electrical solenoid actuators or electromagnets, less than 50 watts @12V continuous duty β R501 & Table 8-1
β Motor/Actuator Power - Each legal motor controller may have one motor connected to the load terminals with exceptions in Table 8-2. Specified motors may be individually connected to Spike or Automation Direct Relay (however multiple pneumatic valves may be driven by a single Spike) β R504, R505 & Table 8-2
β Motor/Actuator Control - Motors/actuators must be controlled by legal motor controllers and driven directly by PWM signals from roboRIO or through legal MXP board or by CAN bus. β R504, R712, R713, R714, R717, R718
The inspector may ask teams to list their motors and describe how they are controlled. They are looking to verify that you are using legal motor/controller models.
β Custom Circuits, Sensors and Additional Electronics - Cannot directly control speed controllers, relays, actuators or servos. Custom Circuits may not produce voltage exceeding 24V. β R614, R625
If the inspector asks about custom circuits, teams should include a description of any cameras and lights on the robot.
β Pneumatic Control Module (PCM) - PCM/PH modules must be connected to roboRIO via CAN bus β R715
β Isolated Frame - Frame must be electrically isolated from battery, roboRIO must be insulated from frame. (>120 Ohm between either PDP/PDH battery post and chassis) β R611
The inspector will ask you to disconnect (but not remove) the battery and close the main breaker. You should remember to open the main breaker after the completion of this test.
The inspector will use a multimeter to measure the resistance between each of the robotβs power connectors and various points on the robot frame.
If the resistance is intermediate (say <1Mβ¦ but >120β¦), the inspector will probably draw this to the teamβs attention. This is a pass for inspection, but may indicate a problem. Common causes include poor grounding on cameras and LED strips.
Pneumatic System using one on-board compressor (n/a for ROBOTS that do not use pneumatics) π
β No Modifications - Actuator mounting pins may be removed, small labels allowed. No painting or large labels. β R803
β Compressor - Only one (on ROBOT only) FRC Legal compressor (max 1.1 CFM flow rate) may be used. β R806
β Compressor Power - Must use a PCM/PH or Relay module β R812 & Table 8-2
β Compressor Control - A Pressure Switch must be wired directly to the PCM/PH or roboRIO to control compressor. β R812
β Vent Plug Valve - Must include an easily-accessible manual vent plug valve to release all system pressure. β R813
β Tubing - Equiv. to KOP with a maximum OD of 1β4β (~6 mm) (documentation may be required). β R804-D
β Gauges - Must be present on both the stored pressure side and working pressure side of the regulator outlet(s) and be readily visible. β R805-E, R810
β Pressure Rating - All pneumatic components at working pressure, must be rated for at least 70 psi (~483 kPa, 4.8 Bar). All components at stored pressure must be rated for at least 125 psi (~862 kPa, 8.6 Bar). β R802
β Valve Control - Pneumatic solenoid valves must have a max 1/8β NPT, BSPP, or BSPT port diameter, be controlled by either a PCM or PH or Relay Module and valve outputs may not be combined. β R804-C, R814 & Table 8-2
Power On Check (Driver Station must be tethered to the ROBOT) π
β Unauthorized Wireless Communication - No wireless communication to/from ROBOT or OPERATOR CONSOLE without prior FIRST written permission. No radios allowed on the OPERATOR CONSOLE or in the pit β R707, R905
The inspector may ask to see your controllers to ensure that you are not using BlueTooth.
β Confirm Pneumatics Operation - With no pressure in system, compressor should start when ROBOT is enabled.
- β Compressor stops - Stops automatically at ~120 psi (~827 kPa, 8.2 Bar) or less under roboRIO control. β R807
- β Check Main Pressure - Must be β€ 120 psi (~827 kPa, 8.2 Bar)
and Working Pressure must be β€ 60 psi (~413 kPa, 4.1 Bar) β [R807](https://frctools.com/2024/rule/R807), [R808](https://frctools.com/2024/rule/R808) - β **Compressor Relief Valve ** - Set to 125 psi, attached to (or through hard fittings) the compressor outlet port. β R811
The relief valve cannot be connected to the compressor using soft tubing.
The inspector will test the compressor relief valve by disabling the pressure sensor. Some valves will whistle when relieving pressure, but not all do this.
- β Relieving Pressure Regulator - Set to β€ 60 psi (~413 kPa, 4.1 Bar), providing all working pressure. β R808
β ROBOT Signal Light(s) - A legal ROBOT Signal Light (two max.) must be easily visible while standing 3 ft. (~100 cm) away from at least one side of the ROBOT, and be plugged into the RSL port on roboRIO. Confirm that the RSL flashes in sync with roboRIO. β R709
β Verify Team Number on DS - Team has programmed the OpenMesh Wireless Bridge at kiosk for this event. β R702
Please remember to take your radio to the kiosk before the inspector arrives in your pit, or it will cause delay.
β Software Versions - The roboRIO image (FRC 2024_v2.1 or later) and DS (24.0 or later) must be loaded β R701, R901
The inspector will verify this by looking at the diagnostics tab on the Driver Station.
β Power Off - Disable ROBOT, then open Main Breaker to remove power from the ROBOT, confirm all LEDs are off, actuate pneumatic vent plug valve and confirm that all pressure is vented to atmosphere and all gauges read 0 psi pressure. β R813
β Driver Console is less than 60β x 14β x 6β6β above floor (approx.). - May have hook and loop hook side attached to secure to Driverβs Station shelf. β R904
Teams are recommended to take advantage of the βhook-and-loop tapeβ on the driver station.
Catching a falling operator console is an exception to G401 (Behind the lines) and G402 (Let the robot do its thing).
Reinspection π
The LRI will typically want to reinspect robots as soon as they have finished their last qualification match and before alliance selection. Commonly RIs will try to direct you to reinspection as you come off the field.
This reinspection is primarily a re-weigh and is typically fast. Usually this is performed with the bumpers from the last match on and the battery out. The LRI will arrange to do the necessary arithmetic to compare this with the initial weigh-in. Remember to release stored pressure from pneumatic systems.
Teams will also be asked if they have made any modifications. Remember that modifications must be reinspected before playing a match (I104, I102).